Project Description:
Petrobras has launched a challenge aimed at reducing exposure to risk in inspection activities in hard-to-reach areas that require working at height or in confined spaces, increasing the efficiency, agility and operational safety of its activities.
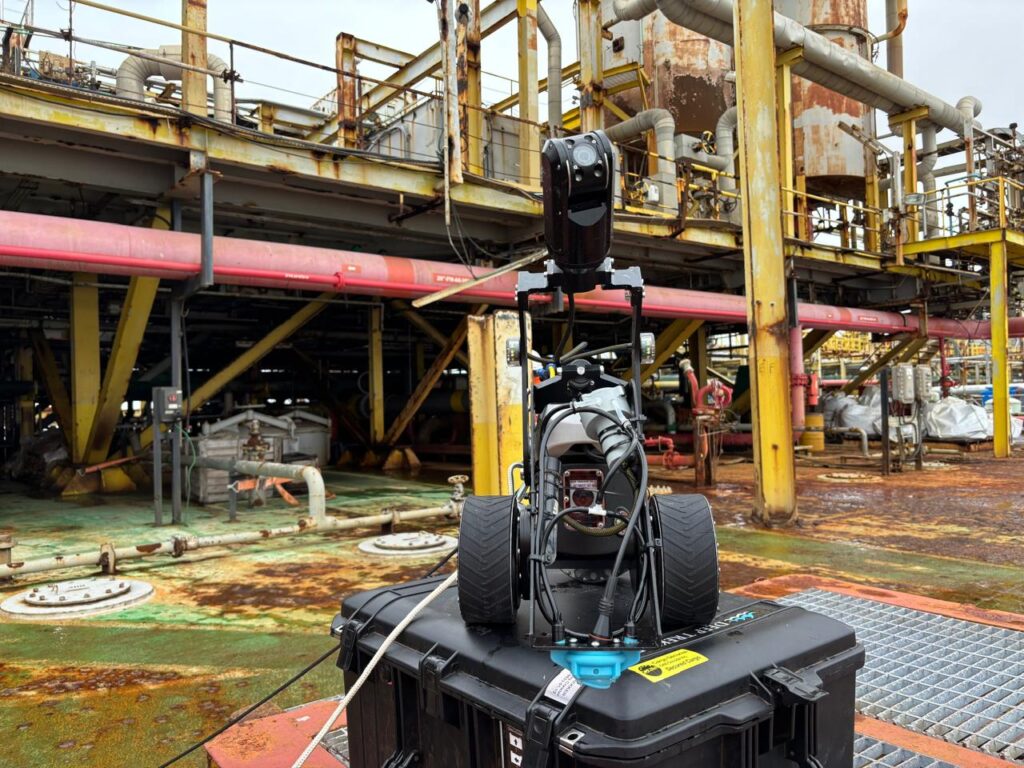
Expected solution:
A system capable of carrying out remote inspections on pipes, equipment and structures that are difficult to access in open areas (working at height, winds, temperatures, etc.), replacing the erection of scaffolding and the work of climbers in visual inspection and thickness measurement activities, based on remotely controlled or autonomous robotic platforms (drones, crawlers, etc.) equipped with their own payload to carry out visual inspection, thickness measurement and crack detection.) equipped with their own payload to carry out visual inspection, thickness measurement and crack detection, and able to operate in open space in onshore and offshore environments, with the possibility of being used in confined spaces.
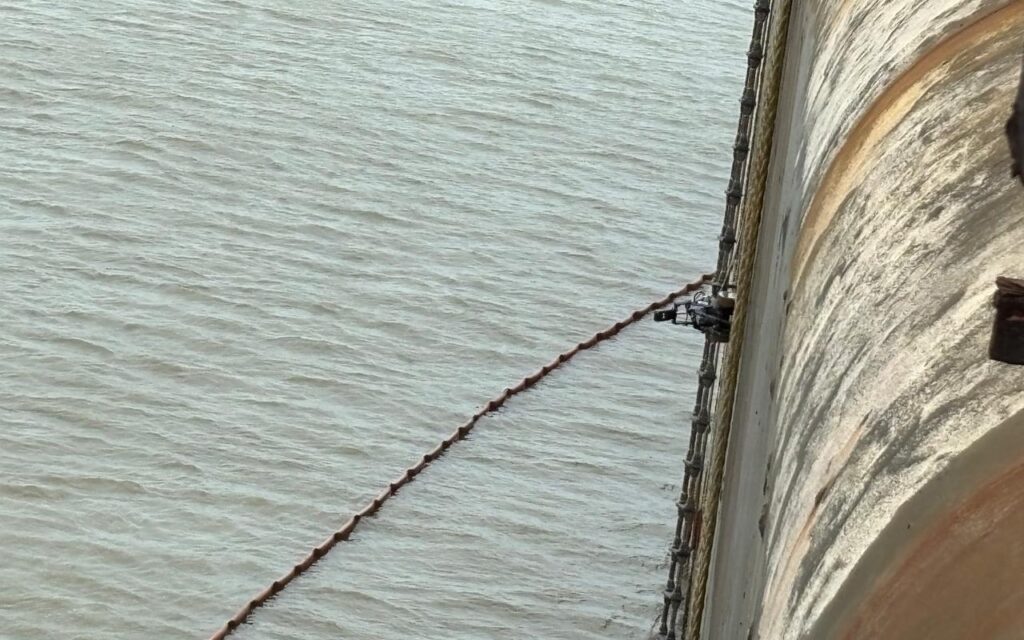
SolutionSolution Implemented:
Submersible Inspection Robot: A vehicle capable of handling the most diverse scenarios, using the same base and controller. It has a magnetic coupling and the ability to carry out a wide range of inspection and cleaning operations, giving versatile operations to a highly portable, battery-operated and easily mobilized vehicle, an essential item for offshore and onshore scenarios.
-
- Predictive Maintenance: Non-destructive testing reports aimed at planning maintenance shutdowns according to the client's needs.
- Supplier management: Coordination with various equipment suppliers to guarantee the availability of parts and specialized technical support.
- Proactive Monitoring: Implementation of a proactive monitoring system to identify and resolve problems before they impact operations.
- Modularity: The robot has peripherals for carrying out visual and measurement inspections in high-risk environments;
- Increased safety: Considerable reduction in the number of workplace accidents in onshore and offshore environments;
- Independence of favorable weather conditions: Operations are subject to weather conditions to carry out the inspection (especially for the offshore industry), the robot can be operated remotely, so its use is independent of weather conditions;
- Cost reduction: From accidents at work and the cost of specialized labor to operate in high-risk environments;
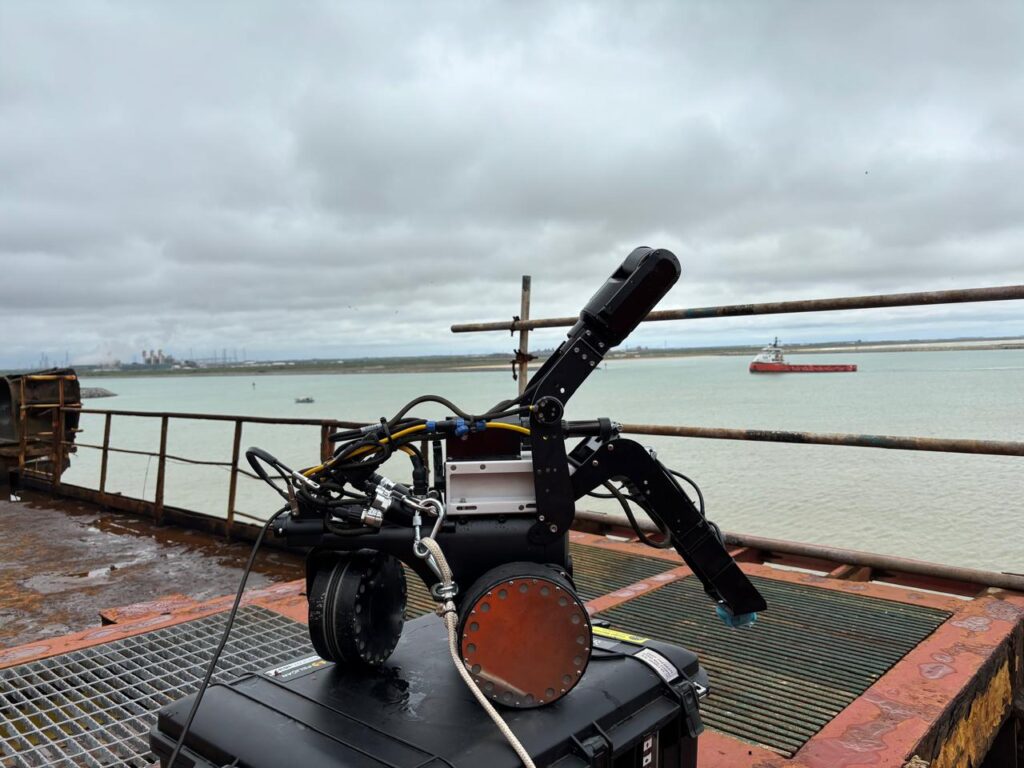
Benefits for Petrobras:
-
- Portability: Easy to mobilize - 3 cases, can be transported on commercial flights;
- Autonomous: requires little/no support from the unit, as the equipment does not need assistance with lifting, power points and/or fine cleaning (although the degree of cleaning will impact on the quality of the inspection);
- Flexibility: Quick and direct integration with the various possible sensors; the same base vehicle can perform several different tasks;
- Real-time evaluation: all visual data can be shared in real time with the client's integrity team, as well as being recorded and documented;
- User-friendly: easy to operate and export/share data;
- Optimized Inspection: Reduction of the risks inherent in the operation, as well as reducing the number of man hours.
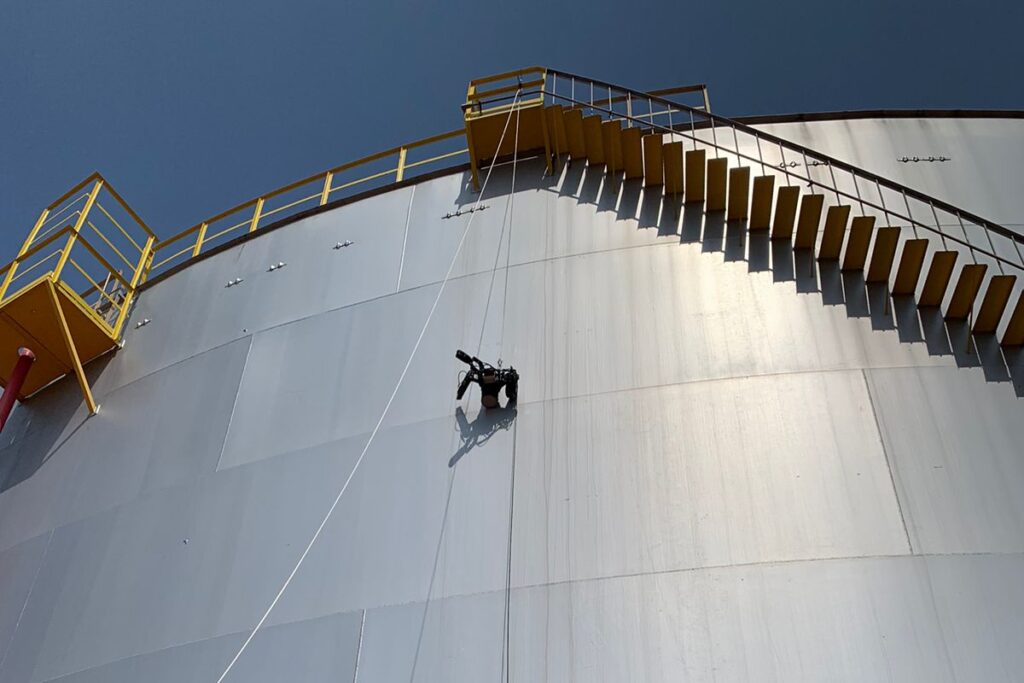